กระบวนการปั๊มเข้ารูปของโลหะแผ่น ข้อดี ข้อเสีย ของการปั๊มงาน
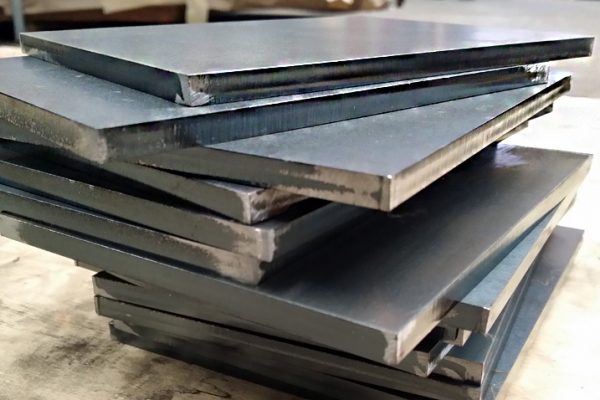
โลหะแผ่น หรือ sheet metal เป็นโลหะที่ถูกนิยามขึ้นตามลักษณะขอพื้นที่ผิวต่อความหนา หากความหนามีมากกว่า 6 มิลลิเมตร จะถูกเรียกว่าเพลท (plate) ซึ่งโลหะแผ่นจะมีความแข็งแรงต่อน้ำหนักสูง ชิ้นส่วนที่ผลิตขึ้นจากโลหะแผ่นจึงมีน้ำหนักที่เบา แต่มีความแข็งแรง สำหรับขั้นตอนการขึ้นโลหะแผ่นจะมีความเกี่ยวข้องกับการเปลี่ยนรูป (deformation) ไม่ว่าจะเป็นการพับหรือการดัด (bending) การปั๊ม (stamping) การยืด (stretching) หรือการขึ้นรูปแบบเย็น (cold-working) ซึ่งจะใช้แผ่นแม่พิมพ์เป็นตัวช่วย และการใช้เครื่องกด (press)
แม่พิมพ์ที่ถูกนำมาใช้ จะเป็นตัวกำหนดการขึ้นรูปร่างของชิ้นงานว่าจะมีขนาดเท่าไหร่ภายหลังเสร็จสิ้น โดยจะประกอบด้วยตัวพั้นซ์ (punch) หรือแม่พิมพ์ และดาย (die) เป็นแม่พิมพ์เช่นกันแต่เป็นตัวเมีย ให้เข้าใจง่ายๆ คือ พั้นซ์จะอยู่ด้านบน ขนาดเล็กกว่าดาย รูปร่างจะคล้ายคลึงกัน และทำหน้าที่เป็นตัวกำหนดเคลื่อนที่เขาหาดาย หลังจากที่ทั้งสองประกบเข้าด้วยกันแล้ว จะเกิดช่องว่างขึ้นมา ส่วนของช่องว่างนี้เองจะถูกกำหนดโดยความหนาของแผ่นโลหะ ชนิด และวิธีการขึ้นรูป
พั้นซ์และดายจะถูกติดตั้งอยู่ในส่วนที่เรียกว่า ใยดายเซ็ท (die set) มีดายอยู่ฐานล่าง (lower die shoe ) และพั้นซ์อยู่ฐานบน (upper die shoe) หน้าที่ของดายเซ็ท จะช่วยให้พั้นซ์และดายเคลื่อนที่เข้าหาและประกบเข้าด้วยกันอย่างถูกต้อง โดยที่ดายเซ็ทจะถูกติดตั้งอยู่บนเครื่องกดที่เรียกว่า “press machine” ส่วนกดยึดอยู่ด้านล่าง ส่วนพั้นซ์ ยึดติดอยู่ด้านบน
ข้อดีจากการกระบวนการปั๊ม
ในทุกกระบวนการที่กล่าวมาข้างต้น การปั๊มจะเป็นกระบวนการที่ดีที่สุดจากทั้งหมด มีข้อได้เปรียบที่เหนือกว่า ไม่ว่าจะเป็นการหล่อ (casting) การทุบขึ้นรูป (forging) และการกัดแต่ง (machining) ซึ่งแบ่งข้อได้เปรียบออกเป็นดังนี้
- ช่วยให้การขึ้นรูปชิ้นงานที่ซับซ้อนได้ง่ายขึ้นกว่าวิธีอื่นๆ
- หลังปั๊มแล้วไม่จำเป็นต้องทำการตกแต่งชิ้นงานแต่อย่างใด
- ชิ้นงานที่ผ่านการปั๊มจะเท่ากันทุกชิ้น สังเกตได้จากการนำเอาชิ้นงานมาประกอบ
- มีความแข็งแรงเพิ่มมากขึ้น รวมถึงคุณสมบัติทางกลอื่นๆ
- ตัวชิ้นงานมีน้ำหนักเบามาก
- อัตราการสามารถทำได้ในปริมาณสูง
ขั้นตอนการทำที่ใช้ในงานปั๊มขึ้นรูป
ในกระบวนการปั๊มขึ้นรูปจะมีหลายกรรมวิธีด้วยกัน หลักๆ จะถูกแบ่งออกเป็น 3 กรรมวิธีตามพื้นฐานทั่วไปคือ
- การตัดเฉือน (shearing) จะแบ่งออกเป็นการปั๊มเจาะ (blaking) และการตัดเจาะรู (piercing)
- การตัด (bending) หรือเรียกว่าการขึ้นรูป (forming)
- การลากเพื่อขึ้นรูป (drawing)
นอกเหนือจากวิธีขั้นพื้นฐานเหล่านี้แล้ว ยังมีการนำเอากรรมวิธีอื่นๆ มาใช้ในกระบวนการเข้ารูปโลหะอเช่น การปั๊มจม (coining) การปั๊มนูน (embossing) การบีบอัด (swaging) การฝานขอบ (shaving) และการตัดขอบ (trimming) ซึ่งการผลิตชิ้นโลหะแผ่นจำเป็นต้องเลือกเอาวิธีที่กล่าวไปข้างต้นมาใช้ โดยจะมีการเลือกกรรมวิธีทำงานดังต่อไปนี้
- Blanking คือขั้นตอนที่ถูกนำมาใช้ในการผลิต ซึ่งจะทำการตัดแผ่นโลหะด้วยพั๊นซ์และดาย เพื่อให้ได้รูปร่างตามที่ต้องการ แผ่นโลหะที่ได้จะถูกนำไปผ่านกระบวนการผลิตในขั้นตอนต่อๆ ไป
- Piercing เป็นขั้นตอนที่ต่อเนื่องมาจาก Blanking โดยการตัดโลหะให้เป็นรูตามจุดที่ต้องการ ซึ่งกระบวนทั้งข้อ 1 และ 2 บางครั้งก็สามารถนำมาทำพร้อมกันได้ในขั้นตอนเดียว แต่ความแตกต่างของทั้งสองคือ blanking จะใช้แผ่นโลหะที่ตัดออกมาด้วยพั๊นซ์และดาย แต่ Piercing จะใช้โลหะที่ถูกตัดเป็นรูนำมาเป็นชิ้นงาน
- Bending คือการตัดพื้นผิวในแนวระนาบขอโลหะ ซึ่งจะช่วยให้เกิดการทำมุมกันตั้งแต่ 1 มุมขึ้นไป โดยที่ระดับความหนาของแผ่นโลหะจะไม่เกิดการเปลี่ยนแปลงใดๆ ส่วนรัศมีการดัดจะมากน้อยก็ขึ้นอยู่กับความหนาของแผ่นโลหะ
- Drawing การขึ้นรูปโดยวิธีลาก โดยการนำเอาพั๊นซ์เข้าไปภายในโพรงของดาย แต่จะไม่มีการยืดแผ่นโลหะเกิดขึ้น ช่องว่างที่เกิดขึ้นระหว่างพั๊นซ์กับดายจึงเท่ากันกับความหนาของแผ่นโลหะ
- Embossing การขึ้นรูปแผ่นโลหะโดยการทำให้เป็นหลุมหรือปุ่มตื้นๆ ความหนาไม่มีการเปลี่ยนแลง นิยมใช้สำหรับการทำแผ่นป้ายที่เป็นตัวอักษรนูนๆ
- Coining การขึ้นรูปแผ่นโลหะโดยการบีบอัดตัวแผ่นโลหะภายในแม่พิมพ์ปิด ทำให้เกิดเป็นลวดลายขึ้นมาทั้งสองด้าน โดยแต่ละด้านอาจจะเป็นคนละลายก็ได้ เช่น การทำเหรียญ เป็นต้น
- Swaging คือการขึ้นรูปโลหะ บีบอัดในแม่พิมพ์แบบเปิด ซึ่งตัวโลหะจะไหลผ่านแม่พิมพ์ออกมาได้อิสระ
- Shaving เป็นกระบวนการตัดแต่งแผ่นโลหะที่ผ่านการ blanking หรือ piercing มาแล้ว
- Trimming กระบวนการทำงานใกล้เคียงกันกับ blanking ซึ่งจะมีการตัดเอาโลหะส่วนเกินทิ้งไป เป็นขั้นตอนหลังสุดภายหลังผ่านกระบวนการอื่นๆ มาเรียบร้อยแล้ว
ประเภทของแม่พิมพ์ที่นำมาใช้งาน
ในการแบ่งประเภทของแม่พิมพ์จะทำการแบ่งตามกรรมวิธี เช่น แม่พิมพ์แบบดัด (bending die) และยังมีการแบ่งตามวิธีทำงาน โดยจะแบ่งได้เป็นประเภทดังนี้ คือ
- แม่พิมพ์แบบธรรมดา (simple die) เป็นแม่พิมพ์ที่ทำงานในการกดเพียง 1 ครั้ง ซึ่งเป็นกรรมวิธีเดียว เช่น blanking เป็นต้น
- แม่พิมพ์แบบผสม (compound die) แม่พิมพ์ที่จะทำหน้าที่ในงานตัด (shearing) สองกรรมวิธีขึ้นไป เพียงแค่กดครั้งเดียวเท่านั้น เช่น การทำ blanking พร้อมกับ piercing ได้ในเวลาเดียวกัน ก็จะได้ชิ้นงานหลุดออกมาจากแถบโลหะ
- แม่พิมพ์แบบรวม (combination die) แม่พิมพ์ที่ทำหน้าที่เหมือนแม่พิมพ์แบบผสม ไม่เพียงทำหน้าที่ในงานตัดเท่านั้น แต่ยังทำงานในส่วนของ bending, drawing และอื่นๆ
- แม่พิมพ์แบบลำดับ (progressive die) แม่พิมพ์ที่ช่วยให้การทำงานพร้อมกันได้ตั้งแต่ 2 กรรมวิธีขึ้นไป ต่างจากแม่พิมพ์ผสมตรงที่กรรมวิธีผ่านแม่พิมพ์จะมีการแยกสถานีออกจากกัน จึงง่ายกว่าแบบแม่พิมพ์ผสม
- แม่พิมพ์แบบชิ้นงานเคลื่อน (transfer die) ระบบที่มีความแตกต่างไปจากแม่พิมพ์แบบลำดับในส่วนของชิ้นงานจะหลุดออกจากแถบโลหะ จากนั้นถูกส่งเข้าไปยังสถานีผ่านก้านโยก (lever) ที่เป็นกลไกเฉพาะ หรือส่วนของลูกเบี้ยว (cam) จะสร้างขึ้นและติดตั้งเอาไว้บนเครื่องกด