ทำความรู้จักชนิด ประเภทของเครื่องกด และงานปั๊ม (Press Machines)
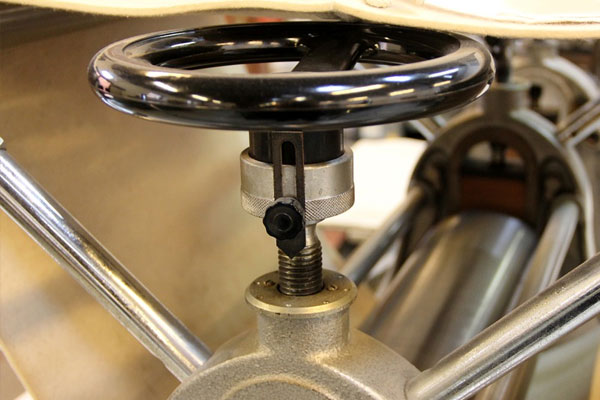
เครื่องกด สามารถจำแนกชนิดได้ด้วยวิธีที่หลากหลาย ตัวอย่างเช่น การจำแนกตามแหล่งให้กำลัง ตามระบบโครงสร้างของเครื่อง ตามจุดมุ่งหมายการใช้งาน หรือตามชนิดก้านกระทุ้ง (ram) เป็นต้น แต่ในที่นี้จะกล่าวถึงชนิดของเครื่องกดที่ถูกจำแนกตามกลไกการถ่ายทอดกำลังแก่ก้านกระทุ้ง โดยสามารถแบ่งแยกกลไกต่างๆ ได้ดังนี้
1. กลไกแบบข้อเหวี่ยง (crank)
กลไกนี้เป็นกลไกที่มีระบบขับเคลื่อนแบบธรรมดา มีการทำงานโดยใช้ข้อเหวี่ยง ซึ่งความเร็วจะมีค่าเพิ่มขึ้นในขณะที่ข้อเหวี่ยงเคลื่อนที่ลง และจะมีค่าความเร็วสูงสุดที่กึ่งกลางของช่วงชัก (stroke) โดยที่ค่าความเร็วสูงนี้สุดจะเกิดการกดแม่พิมพ์ขึ้น
2. กลไกแบบเยื้องศูนย์ (eccentric)
กลไกนี้จะมีการทำงานเหมือนกับกลไกข้อเหวี่ยง (crank) แต่มีความแข็งแรงและมีช่วงชักที่สั้นกว่า
3. กลไกแบบลูกเบี้ยว (cam)
มีกลไกการทำงานคล้ายกับกลไกแบบเยื้องศูนย์ (eccentric) แต่มักถูกใช้กับการเคลื่อนที่ของramพิเศษ ตามความเหมาะสมและการใช้งาน
4. กลไกแบบเฟืองรางและเกียร์ (rankandgear)
เป็นกลไกที่มีจังหวะการเคลื่อนที่สม่ำเสมอ และสามารถควบคุมช่วงชักได้ ตัวหยุดถูกนำมาใช้สำหรับการทำงานที่ต้องการช่วงชักที่มีความยาวมาก แต่มีข้อเสียคือจะช้ากว่ากลไกแบบข้อเหวี่ยง (crank) ซึ่งกลไกนี้สามารถติดตั้งอุปกรณ์ quick-return สำหรับช่วย ram ในการเคลื่อนที่กลับไปยังจุดเริ่มต้นให้เร็วมากขึ้น
5. กลไกแบบไฮดรดลิก (hydraulic)
เป็นกลไกที่เคลื่อนที่ช้าแต่ให้แรงกดมาก ถูกนำไปใช้ในเครื่องกดและงานต่างๆ โดยเฉพาะสำหรับงาน drawing และ forming
6. กลไกแบบข้อต่อร่วม (knucklejoint)
เป็นกลไกที่มีค่าความได้เปรียบทางกลสูง จึงได้รับความนิยมมาก ซึ่งเหมาะสำหรับการทำ coining และ sizing เนื่องจากสามารถให้แรงกดมากที่ระบบยืดสุด
7. กลไกแบบข้อศอก (toggle)
เป็นกลไกที่ใช้ถูกใช้สำหรับในขั้นตอนการยึดแผ่นโลหะ (blank-holder) ของงาน drawing เป็นหลัก ซึ่งตรงกับจุดประสงค์หลักของการออกแบบคือการยึดและจัดตำแหน่งของแผ่นโลหะให้เหมาะสม
8. กลไกแบบสกรู (screw)
กลไกนี้ใช้แผ่นจานเสียดทาน (frictiondisk) เป็นระบบขับเคลื่อนหลักสำหรับการขับเคลื่อนล้อตุนกำลัง(flywheel) ด้วยค่าความเร็วสูง โดยล้อตุนกำลังจะสะสมพลังงานแล้วถ่ายทอดลงชิ้นงานที่ระยะยืดสุดกำลัง
เครื่องกดที่ใช้ระบบกลไกด้วยล้อตุนกำลัง (flywheel) จะเหมาะสำหรับงาน blanking และ drawing เนื่องจากกลไกนี้สามารถให้แรงกดได้ตั้งแต่ 20-6,000 ตัน มีค่าความเร็ว 20-1,500 ครั้งต่อนาที และมีช่วงชักตั้งแต่ 5-500มิลลิเมตร ส่วนเครื่องกดที่ให้กำลังด้วยระบบไฮดรอลิกนั้น เหมาะสำหรับงานที่ใช้ combination die และงานdeep drawing เนื่องจากเป็นกลไกที่สามารถให้แรงกดได้สูง ตั้งแต่ 20-10,000 ตัน มีช่วงชักตั้งแต่ 10-800มิลลิเมตร โดยที่สามารถให้กำลังเต็มที่ได้ทุกระยะของช่วงชัก
ลักษณะของชิ้นงานปั๊ม
ในกระบวนการปั๊มสามารถให้ชิ้นงานที่มีความหนาสม่ำเสมอและคงที่ได้ แต่จะมีข้อยกเว้นในบางกรณี ซึ่งรูปร่างของชิ้นงานที่กระบวนการปั๊มทำได้ จะเริ่มต้นตั้งแต่รูปร่างแบบธรรมดาไปจนถึงแบบซับซ้อน มีขนาดเริ่มต้นตั้งแต่เล็กเท่าชิ้นส่วนนาฬิกาข้อมือไปจนถึงใหญ่เท่ากับเครื่องบินหรือตัวถังรถบรรทุก และมีความหนาตั้งแต่ 0.025มิลลิเมตร ถึง20มิลลิเมตร ซึ่งค่าความหนาปกติมักอยู่ระหว่าง 1.3 มิลลิเมตร ไปจนถึง 9.5 มิลลิเมตร หลังจากที่ชิ้นงานผ่านเข้าสู่กระบวนการปั๊มแล้วจะสามารถแบ่งแยกลักษณะของชิ้นงานได้ ดังนี้
1. ขอบหนาม (burr-side) และรัศมีการตัด (cut radius)
เป็นการเกิดลกษณะผิวคล้ายหนาม ขรุขระไม่เรียบที่บริเวณขอบรอยตัดด้านหนึ่งของแผ่นโลหะ ลักษณะที่เกิดขึ้นเรียกว่า burr-side ส่วนในด้านตรงข้ามนั้นขอบรอยตัดจะเกิด rollover คือเกิดรัศมีการตัด ซึ่งสามารถใช้กรรมวิธี deburring เข้ามาแก้ไขได้ โดยลักษณะดังกล่าวจะพบในการตัดแผ่นโลหะด้วยวิธี piercing หรือ blanking
2. Concentricity
เป็นลักษณะของการที่จุดศูนย์กลางเส้นรอบรูปวงในและวงนอกเกิดการเยื้องกันเล็กน้อย โดยลักษณะดังกล่าวนี้จะพบได้ในทุกกระบวนการปั๊ม ยกเว้นการใช้ compound die ที่สามารถยอมรับชิ้นงานได้หากค่าความคลาดเคลื่อนมีค่าไม่เกินที่กำหนดไว้
3. Flatness/Blanking Distortion
เป็นลักษณะที่ชิ้นงานเกิดการโก่งงอเล็กน้อยจากปริมาณแรงเค้นและแรงกด โดยจะขึ้นอยู่กับชนิดของวัสดุ รูปร่าง ขนาดของพื้นที่ผิวและความหนาของชิ้นงาน ซึ่งการโก่งงอนี้เป็นปัญหาที่ส่งผลต่อการควบคุมความแบนราบ ฉะนั้นหากต้องการให้ชิ้นงานมีความแบนราบมากที่สุดจึงสามารถใช้ compound die ได้
ข้อแนะนำในการออกแบบชิ้นงานปั๊ม
ในการออกแบบชิ้นงานปั๊มที่ดีนั้น ต้องคำนึงถึงการนำวัตถุดิบมาใช้ให้เกิดความคุ้มค่าและประโยชน์สูงสุดโดยที่ไม่เกิดของเสียขึ้น ฉะนั้นลำดับขั้นตอนการผลิตที่ในปัจจุบันยังมีข้อจำกัดของกรรมวิธีต่างๆ จึงเข้ามามีบทบาทสำคัญในการสร้างชิ้นงานที่ดี สามารถแบ่งแยกข้อแนะนำการใช้งานของกรรมวิธีหลักๆ ได้ดังนี้
Blanking
- แผ่นโลหะควรมีความหนามากกว่า 0.8 มิลลิเมตร และชิ้นงานควรมีมุมมองที่มีรัศมีอย่างน้อย 0.5 เท่าของความหนาแผ่นโลหะ
- ระยะความกว้างของ Tab และ slot ควรมีค่าไม่ต่ำกว่า 1.5 เท่าของความหนาแผ่นโลหะ และควรมีความยาวไม่เกิน 5 เท่าของความกว้าง
- ควรหลีกเลี่ยงการปั๊มส่วนครึ่งวงกลมโค้งที่มีระยะผ่านศูนย์กลางเท่ากับระยะกว้างของแผ่นโลหะ
Piercing
- ระยะเส้นผ่านศูนย์กลางของรู ควรมีค่ามากกว่าหรือเท่ากับความหนาของแผ่นโลหะ ซึ่งสำหรับเหล็กสเตนจะมีค่าเท่ากับ 2 เท่า
- รูควรมีระยะห่างเท่ากับหรือมากกว่า 2 เท่าของความหนาแผ่นโลหะ
- ระหว่างชิ้นงานกับรู ควรมีระยะห่างอย่างน้อยเท่ากับความหนาแผ่นโลหะ
Bending
- เพื่อป้องกันการแตกตามรอยพับ ควรให้แนวรอยพับตั้งฉากกับแนวการกรีดหรือแนวเกรนของแผ่นโลหะ
- การป้องกันรูบิดเบี้ยว ระยะห่างระหว่างรอยพับกับรูควรมีค่าอย่างน้อย 1.5 เท่าของความหนาแผ่นโลหะรวมกับรัศมีการพับ
- ด้านในควรมีมุมการพับเท่ากับ 90 องศา
- สำหรับการพับรูป Channel ควรมีความกว้างเท่ากับ 3 เท่าของความหนาแผ่นโลหะและมีระยะความกว้างต่อความสูงอย่างน้อย 2:1
การลดเศษวัสดุจากกระบวนการผลิต นอกจากจะทำได้โดยการปฏิบัติตามข้อแนะนำกรรมวิธีการผลิตแล้ว สิ่งที่สำคัญอีกอย่างหนึ่งก็คือการจัดเรียงชิ้นงานบนแผ่นโลหะให้สามารถประหยัดวัตถุดิบได้มากที่สุด อีกทั้งการลำดับขั้นตอนการผลิตก็เป็นวิธีหนึ่งที่สามารถช่วยลดของเสียได้เช่นเดียวกัน